About HDD
Horizontal directional drilling is a trenchless construction method utilizing boring equipment and techniques to install utilities such as fiber optic, electric cables, and water and sewer pipelines where conventional open trench construction is not feasible or will cause adverse disturbances to environmental features, land use or physical obstacles. Horizontal directional drilling (HDD) has emerged as a preferred method of installation of utilities under waterways, roadways, rail lines, congested infrastructure areas and other environmentally sensitive areas. This technology has been enthusiastically embraced as a low impact construction technique because it reduces interruption to traffic and disturbance to landscape and existing surfaces.
HDD is performed in the following phases:
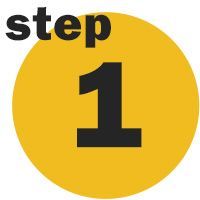
Bore Planning
We first determine whether we can safely and successfully bore by studying available geological data and conducting field investigations. We assess obstacles and constraints of the surface set up area, the location of existing utilities, and signs of potential subsurface conditions likely to be encountered. If we consider that HDD is feasible, we design a drill path to meet the specifications and select appropriate drill entry and exit locations.
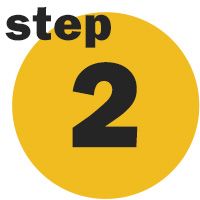
Subsurface Investigation
Utilities in the work area are located prior to any excavation. Vacuum potholing is used to verify depths of the utilities in proximity to the bore path. Once all utility depths have been verified, the bore profile plan is adjusted to ensure that proper clearance is given to the existing utilities.
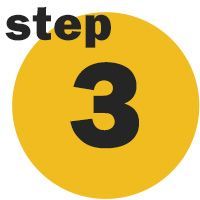
Drilling the Pilot Hole
An HDD drill rig and supporting water tank and mud mixing equipment are set-up at the drill entry location determined during the pre-site planning phase. A pilot hole is drilled along the predetermined drill path. This process begins when the directional drill machine pushes a bore head connected to hollow pipe into the ground at an angle. As each joint of drill pipe is pushed into the ground a new one is added behind and the joints torqued tight using a hydraulic vise. Periodic readings from a walk over locating system are used to determine the horizontal and vertical coordinates along the pilot hole. Drilling fluid is injected under pressure ahead of the drill bit and transport drill cuttings to the surface, clean build-up on the drill bit, cool the drill bit, reduce the friction between the drill and bore wall, and stabilize the bore hole. Vacuum potholing equipment is used to keep returned drill slurry from the bore pits to keep the work area clean.
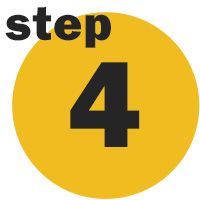
Reaming of the Pilot Hole
The down hole drill bit assembly is removed from the drill string upon breaking the ground surface at the exit pit location and is replaced with a back reamer or hole opener for rock. The drill string is pulled back through the bore hole and the back reamer enlarges the diameter of the drill hole. The reamer may be pulled from the pipe side of the HDD crossing if additional passes with the reamer are required to achieve the desired bore hole diameter. The reaming stage may not be necessary during HDDs for small diameter conduit installations where the bore hole created by the pilot hole drill is of adequate size to pull back the pipe string.
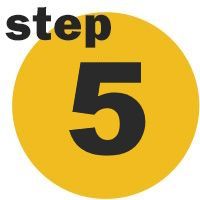
Pipe Pull back
The pipe is attached to the drill string with a swivel and reamer and pulled back into the bore hole. Pull back continues until the entire pipe has been pulled into the bore hole. Upon successful pull back of the pipe string, the drilling equipment is dismantled and demobilized.